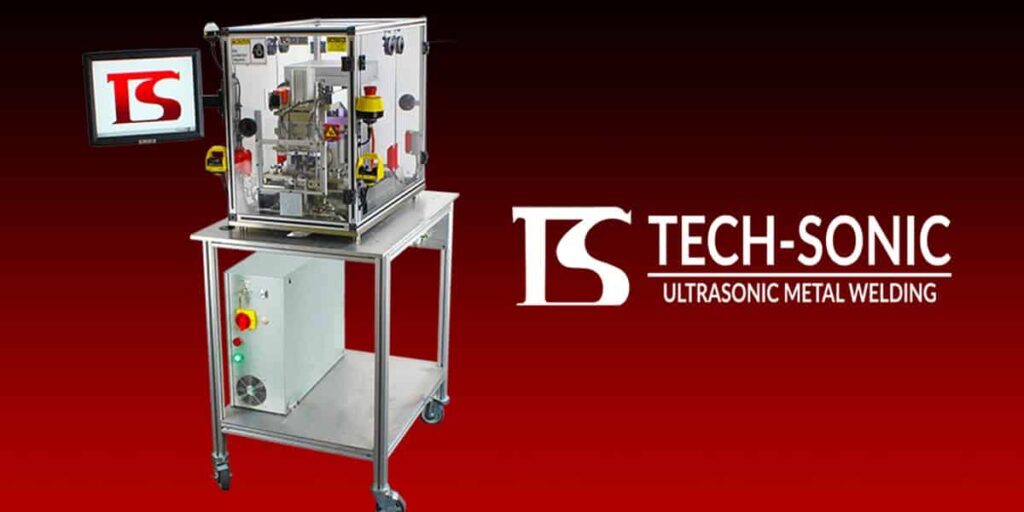
Ultrasonic Welding Technology: What is it for?
Joining metals has come a long way from traditional techniques such as soldering, using bolts, nails, or even adhesives. In this digital age, ultrasonic welding technology is developed because of the increasing call for high-quality electronics.
What is Ultrasonic Welding Technology?
Ultrasonic welding technology is different from lower temperature methods of joining metals such as soldering. It is because it does not melt the metal. It utilizes other metals or thermoplastics at high heat to fuse solids.
Ultrasonic metal welding is the better choice for fusing solids such as metals. It uses energy from ultrasonic vibrations to create friction-like motions. This produces heat that joins two surfaces smoothly and quickly. It’s high-frequency, low-amplitude vibration cause materials to bond on a molecular level.
This type of method also bonds dissimilar materials. Examples are brittle glass to hard metals or steel to aluminum. The ultrasonic welding technology is also ideal for welding materials with high thermal conductivity like copper or aluminum since there is less distortion.
Advantages of Ultrasonic Welding Technology
One of the most widely used welding techniques in the industry is ultrasonic welding. It has several key advantages over other types of welding. Some of these ultrasonic welding advantages are below:
- Cost-Effective
- Safe
- Reliability
- Joint Quality
- Speed
- Precise
Ultrasonic Welding Applications
This ultrasonic welding technology has many applications. Many industries especially those using complex, delicate, or minuscule components utilize this method. It is commonly used in:
1. Medical industry
One of the most successful applications is in the integrated circuit connections of medical devices. There is no need for glue or adhesives since it uses the machine’s material in forming a bond. It is used in manufacturing heart sensors for bypass patients. It is also used in fabricating intravenous catheters, blood/gas filters, dialysis machines, valves, and filters.
2. Electronics and computer industry
Microelectronic components are best joined using ultrasonic welding technology. This includes microchips, electric motors, capacitors, flash drives, computer disks, microprocessors, transformers. Ultrasonic metal welding is perfect for welding high-thermal-conductivity materials such as aluminum and copper. This process bonds thin to thick materials and seamlessly joins wires and circuitry. It bonds electrical connections on computer circuit boards without effort and is well-suited to the smartphone and computer industry.
3. Automobile and aerospace industry
A popular choice in manufacturing engine components, instrument panels, steering wheels, and interior panels. The ultrasonic welding technology has the ability to join non-ferrous materials such as aluminum to steel contributing to strong, visually appealing, and dimensionally precise parts and components. It also fulfills the need for tautness and burst resistance for airtight compartments.
Related Topic:
|
4. Refrigeration and Air Conditioning
Traditionally, this industry has been using copper tubes in its cooling systems. But there is now a shortage of this expensive material. That is why the cheaper aluminum tube has become an appealing and viable alternative. Applying ultrasonic welding technology to this drawback has made this possible. A more reliable solution is using the Ultrasonic Tube Sealer Machine by TECH-SONIC, Inc. This US-3620TS-EX ultrasonic tube sealer is an energy-efficient machine. It is one of the proven solutions in the refrigeration industry today.
Related Topic:
|
5. Packaging industry
The ultrasonic welding technology is ideal for packaging since there are no noticeable seams. It welds materials without any impurities or thermal distortions. Fabrication of blister packs, metal capsules, containers for hazardous or heat-sensitive substances is rapid and efficient. It is also more sanitary since there are no binding agents and solvents to dry or substances to cure.
6. Consumer industry
This eco-friendly process can effectively create a hermetic seal in processing food. It bonds contact points that are difficult to reach using other welding methods and is also used to manufacture a variety of products, including mechanical toys, butane lighters, and mobile phones.
Conclusion
Using ultrasonic welding technology results in high-quality products. It helps manufacturers to outclass their competitors. Investing in this ultrasonic welding technology helps increase production. Thus, ultrasonic welding is expected to propel market growth across many industrial applications.
What is the difference between Ultrasonic Welding vs. Conventional Welding? Read the article to know its differences, pros, and cons.
Featured Products
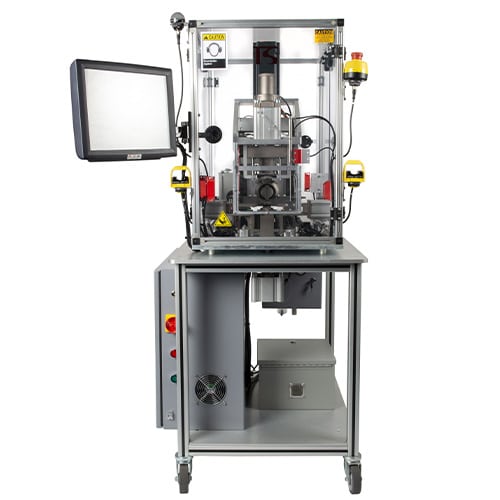
CLC Large Cable Termination Welder
US-3620STH
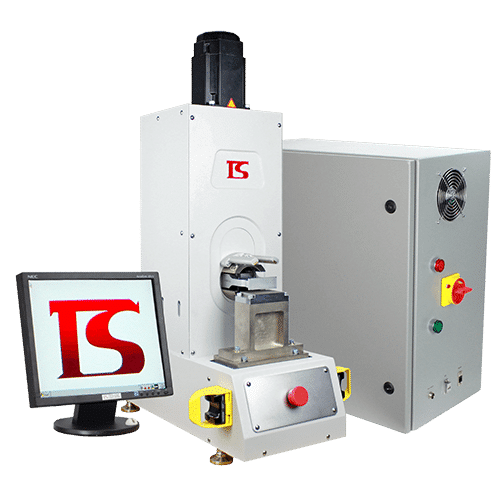
CLC Pouch/Prismatic Battery Welder
US-3620SH
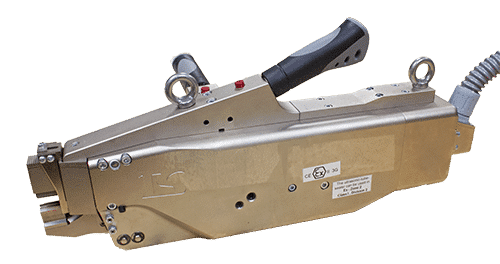
Ultrasonic Tube Sealer (Explosion Proof)
US-3620TS-EX