Wire Splicing for Automotive Applications
USCAR-45 defines test methods and performance requirements for ultrasonically welded wire-to-wire splicing for automotive applications. The tests defined in this specification subject samples on tests to stresses that simulate a lifetime of exposure for a road vehicle. Stresses include Thermal shock, Temperature and Humidity cycling, and Mechanical Abuse. With the growing market of Electric Vehicles, quality control for wire splicing is becoming more important to ensure the functionality of the electrical components in Electric Vehicles EV. In compliance with USCAR-45, the 3620WS2P ultrasonic wire splicing machine has the ability to detect 3% of missing strands of total cross section area.
Ultrasonic welding technology is widely used to create electrical components in the automotive industry, as well as other manufacturing sectors. Electrical components are usually welded with a traditional pneumatic cylinder, however, TECH-SONIC’s patent-pending closed-loop control (CLC) ultrasonic wire splicing, US-3620WS2P, goes far beyond conventional pneumatic welding. This wire splicing machine combined with a Servo Motor and embedded high-speed digital microprocessor control, allows for monitoring of force feedback sensors for precise welding. Its unique features are also revolutionizing the wire splicing industry with its small wire splicing capability and industry leading missing strand detection.
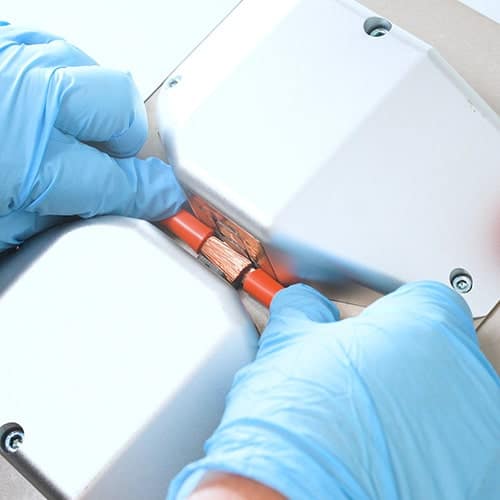
CLC Advantages for Ultrasonic Wire Splicing
Conventional pneumatic wire splicers require the application of higher pressure and ultrasonic power to overcome energy losses. They also cause additional stress on the tooling by using excessive force, diminishing the life of the horn and anvils, and often resulting in wire breakage due to excess stress on strands. Using ultra-high-speed digital control, the US-3620WS2P, provides Dynamic Force and Amplitude Control™ with multi-step welding and real-time force monitoring. This produces optimum welding conditions by adjusting both power and force so it can weld wires of many different sizes and provide better quality welds. Employing force feedback via precise Closed-Loop Control, the US-3620WS2P wire splicer can also detect missing strands more accurately and consistently than a pneumatic wire splicer, below 3% of the total cross section. Automobile manufacturers require the wire harness producers to detect less than 3% of missing strands.
Benefits and Features of Closed Loop Control Technology for Wiring Splicing
- In compliance to USCAR-45, ability to detect 3% of missing strands of total cross section area
- Cross section area .13mm2 – 48mm2
- 22 inch touch screen display (CLQC)
- Capability of up to 20 weld steps instead of traditional single step
- Ability to change and adjust force and amplitude during weld cycle
- Measurement of pre-weld and post-weld height (CLQC)
- Less power / lower operational cost
- Longer tooling life due to “patented” Servo Control technology
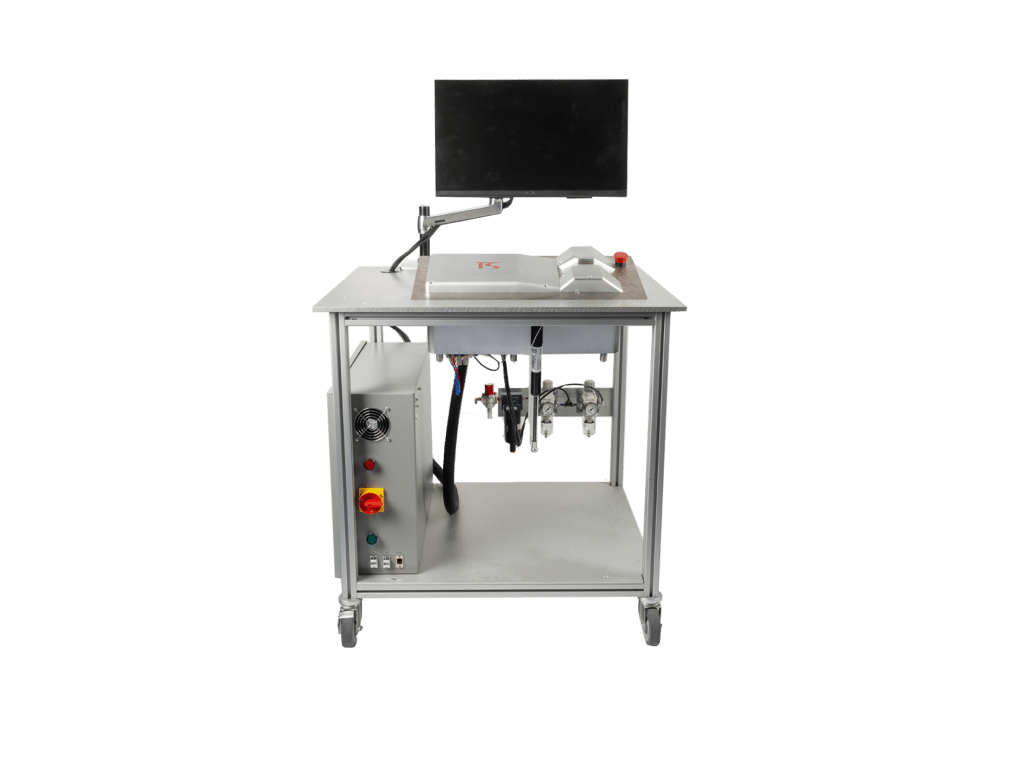
For more technical information, please download our brochure.
US-3620WS2P SAMPLES
Related Products
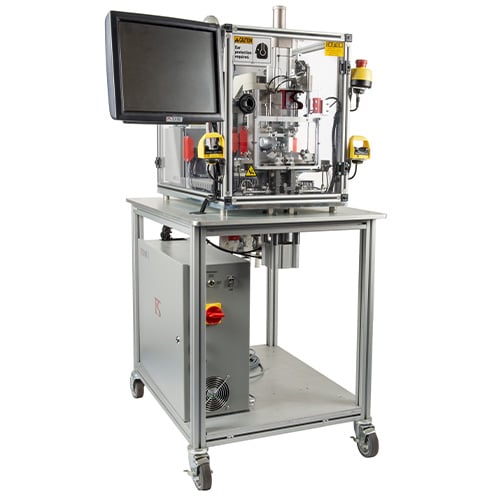
CLC Ultrasonic Ring Termination Machine
US-3620SRT
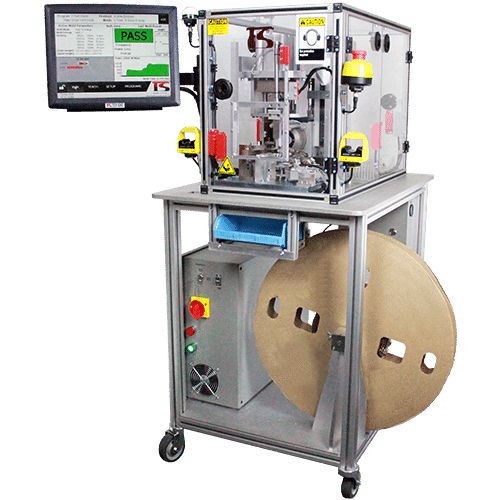
CLC Reel-Feed Terminator
US-3620MAK-S
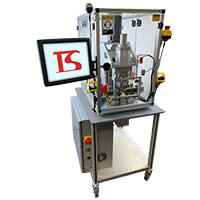
CLC Large Cable Termination Welder
US-3620STH